Heavy duty
- Home
- Heavy duty
Industris Services
BROCHURES
Download your Free Report: What every business owner must know
Download Brochures PDFGET A QUOTE
YPU NEED TO KNOW ABOUT
HEAVY DUTY
Heavy-duty lubricants refer to specialized lubricating oils and greases designed to provide effective lubrication and protection in demanding and high-stress applications, typically involving heavy machinery and equipment. These lubricants are formulated to withstand extreme conditions, such as high temperatures, heavy loads, and severe operating environments. Here are some key aspects to consider when discussing heavy-duty lubricants:
High Viscosity: Heavy-duty lubricants often have a higher viscosity compared to standard lubricants. This allows them to maintain a protective film between moving parts under heavy loads, preventing metal-to-metal contact and reducing wear.
Extreme Pressure (EP) Additives: Heavy-duty applications often involve extreme pressure conditions, where conventional lubricants may fail. EP additives are incorporated into heavy-duty lubricants to provide additional protection under high-pressure situations, ensuring that the lubricant can withstand extreme loads without breaking down.
Heat Resistance: Heavy machinery and industrial equipment can generate significant heat during operation. Heavy-duty lubricants are formulated to resist thermal breakdown, maintaining their effectiveness at high temperatures and preventing the formation of sludge and deposits.
Corrosion and Rust Protection: Many heavy-duty lubricants include additives that protect against corrosion and rust. This is particularly important in harsh environments where machinery is exposed to moisture or corrosive substances.
Water Resistance: Some heavy-duty applications involve exposure to water or other fluids. Lubricants designed for these conditions are formulated to resist emulsification and maintain their lubricating properties even in the presence of water.
Longer Service Intervals: Heavy-duty lubricants are often engineered to provide longer service intervals, reducing the frequency of lubricant changes and maintenance, which is crucial in industries where downtime is expensive.
Compatibility with Seals and Gaskets: Heavy-duty lubricants must be compatible with the materials used in seals and gaskets within the machinery. Compatibility ensures that the lubricant does not degrade these components, maintaining their integrity and preventing leaks.
Viscosity Index (VI): A high viscosity index indicates that the lubricant’s viscosity changes less with temperature variations, providing stable lubrication across a broad temperature range.
Applications for heavy-duty lubricants include mining equipment, construction machinery, agricultural machinery, industrial gearboxes, and various types of heavy-duty vehicles such as trucks and buses.
Choosing the right heavy-duty lubricant for a specific application is essential for ensuring the longevity and optimal performance of the equipment. Manufacturers often provide guidelines and specifications to help users select the appropriate lubricant for their particular machinery and operating conditions.
- Construction of hydroelectric reservoirs
- Installation of equipment and exploitation of wind energy
- Installation of equipment and exploitation of solar energy
- Manufacturing and manufacturing generators
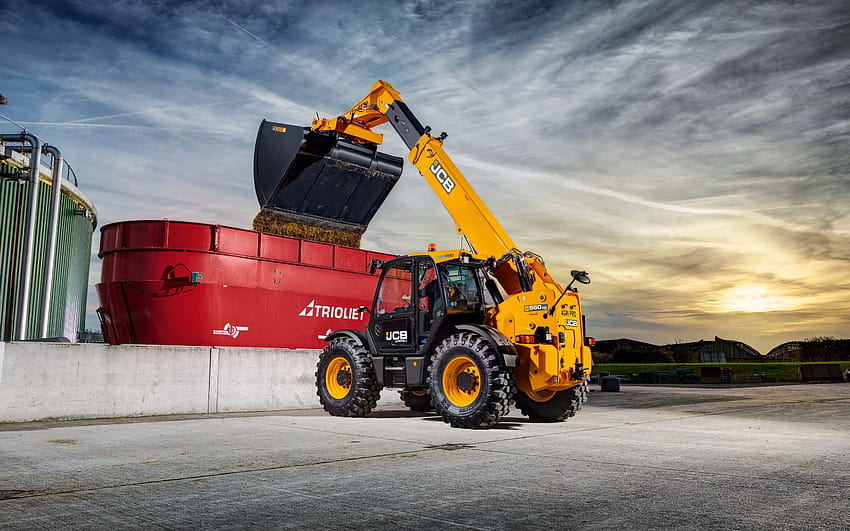